Mastering Styrenic Stabilization for Enhanced Industrial Applications
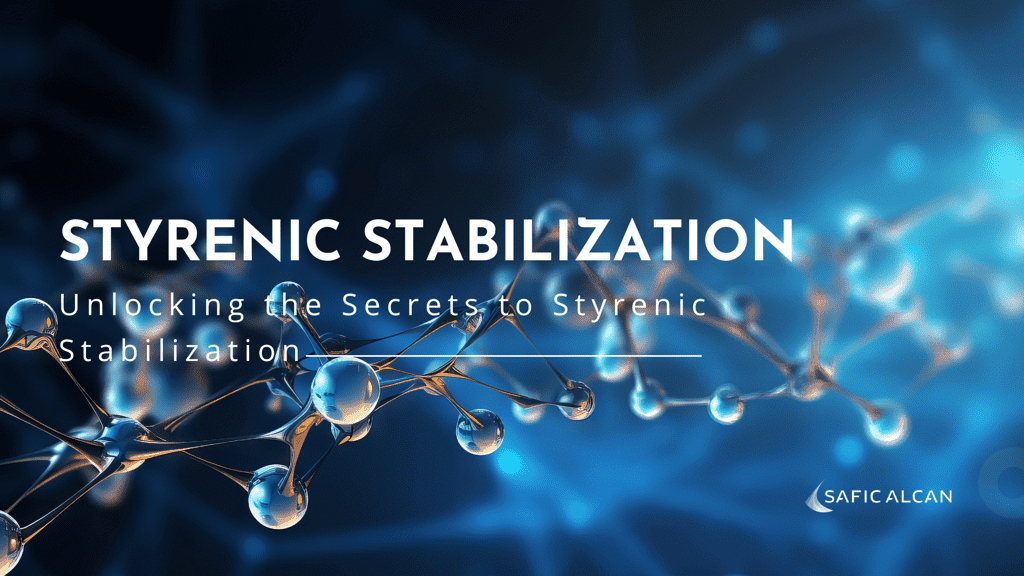
Styrenics have become an indispensable part of modern industrial manufacturing. From food packaging to electronics, their versatility is unmatched. But the magic behind their performance lies in their stabilization.
The Impact of Thermal Oxidation on Polymers
If you're a plastics engineer or an industrial manufacturer, understanding how to stabilize Styrenic polymers can elevate your projects to new heights. In this blog post, part of our Antioxidant series, which started by discussing the role of antioxidants in polymer chemistry, moving further in detail to polyolefin stabilization, we’ll now explore key techniques and strategies for stabilizing different types of Styrenics, offering practical tips and insights to ensure you achieve the best results.
Introduction to the World of Styrenics
Styrenics are a family of plastics widely used across various industries. Known for their versatility and durability, these polymers include crystal polystyrene, styrene-acrylonitrile (SAN), high-impact polystyrene (HIPS), and acrylonitrile-butadiene-styrene (ABS). Each type has unique properties and stabilization requirements, making them suitable for different applications.
Why Stabilization is Crucial for Styrenic Polymers
Stabilization is essential to prevent degradation during processing and usage. Without proper stabilization, styrenics can suffer from discoloration, loss of mechanical properties, and other issues that compromise their performance. Effective stabilization ensures that these polymers maintain their integrity and functionality over time.
Stabilization of Crystal Polystyrene
Understanding Crystal Polystyrene
Crystal polystyrene is a transparent polymer known for its clarity and rigidity. It is commonly used in applications such as food packaging, disposable cutlery, and laboratory ware. However, high temperatures during processing can lead to degradation and a loss of molecular weight.
The Role of Antioxidants
To enhance the thermal stability of crystal polystyrene, antioxidants like Euronox 76 are added during polymerization. A concentration of 1000 ppm is typically sufficient to prevent degradation and maintain the polymer's molecular weight.
Practical Application
Adding antioxidants during polymerization helps prevent thermal degradation, ensuring that crystal polystyrene retains its mechanical properties and clarity. This makes it an ideal choice for applications where transparency and rigidity are crucial.
Optimizing Stabilization for Styrene/Acrylonitrile (SAN) Copolymers
Challenges with SAN
Styrene/acrylonitrile (SAN) copolymers are valued for their toughness and chemical resistance. However, they are prone to discoloration under heat stress, even in the absence of oxygen. This can limit the effectiveness of antioxidants.
Effective Antioxidant Combinations
To combat discoloration in SAN, a combination of antioxidants is often used. For example, using 200 ppm of Euronox 76 and 800 ppm of Euronox. 168, or alternatively 1000 ppm of Euronox. B14, can effectively stabilize SAN under heat stress.
Implementation Strategies
By incorporating these antioxidant combinations, you can significantly reduce the risk of discoloration and maintain the aesthetic and functional properties of SAN copolymers in various applications, from automotive parts to household items.
Enhancing Stability of High-Impact Polystyrene (HIPS)
Understanding HIPS
High-impact polystyrene (HIPS) is a toughened version of polystyrene, made by adding rubber-like polymers to improve impact resistance. It is frequently used in products like toys, appliances, and electronics housings. However, HIPS is susceptible to thermal oxidative degradation, leading to yellowing and reduced mechanical properties.
Importance of Elastomeric Phase Stabilization
The degradation primarily affects the elastomeric phase, which constitutes about 10% of the polymer weight. Therefore, it is crucial to add stabilizers during the polymerization process rather than before pelletizing.
Recommended Stabilizers
Introducing 500-1500 ppm of Euronox 76 can provide adequate protection against discoloration and prevent undesired crosslinking of the elastomer during polymerization. This ensures that HIPS maintains its impact resistance and aesthetic appeal.
Advanced Stabilization Techniques for ABS Terpolymers (Acrylonitrile/Butadiene/Styrene)
Characteristics of ABS
ABS is a versatile polymer known for its excellent toughness, impact resistance, and ease of processing. It is used in a wide range of applications, including automotive parts, consumer electronics, and healthcare products. ABS typically contains around 30% elastomeric phase.
Production Processes
ABS can be produced through bulk polymerization or emulsion polymerization, with the latter accounting for over 90% of commercially available ABS. In emulsion polymerization, the elastomeric and hard phases are prepared separately and then blended via compounding.
Stabilization Techniques
To stabilize the rubber phase of ABS, a combination of primary and secondary antioxidants is commonly used. Effective antioxidants include Euronox 76, Euronox.245, and Euronox.DL. These antioxidants are added as emulsion or dispersion before the coagulation, isolation, and drying processes.
Additional Stabilization for Extrusion ABS
For extrusion ABS types intended for pipes and sheets, additional stabilization during compounding is necessary. Effective stabilizers for this purpose include Euronox.565 and Euronox.DL, ensuring that the polymer retains its mechanical properties and durability during the extrusion process.
Understanding the stabilization of different types of styrenics is crucial for plastics engineers and industrial manufacturers aiming to optimize their products' performance and longevity. By incorporating the right antioxidants and stabilization techniques during polymerization and processing, you can prevent degradation, discoloration, and loss of mechanical properties.
Incorporate these insights into your manufacturing processes, and you'll be well on your way to producing high-quality, stable styrenic polymers that meet the demands of various industrial applications. For further guidance and expert advice on stabilizing styrenics, consider consulting with industry professionals and staying updated with the latest advancements in polymer stabilization.