Polyamide Stabilization in Engineering Plastics
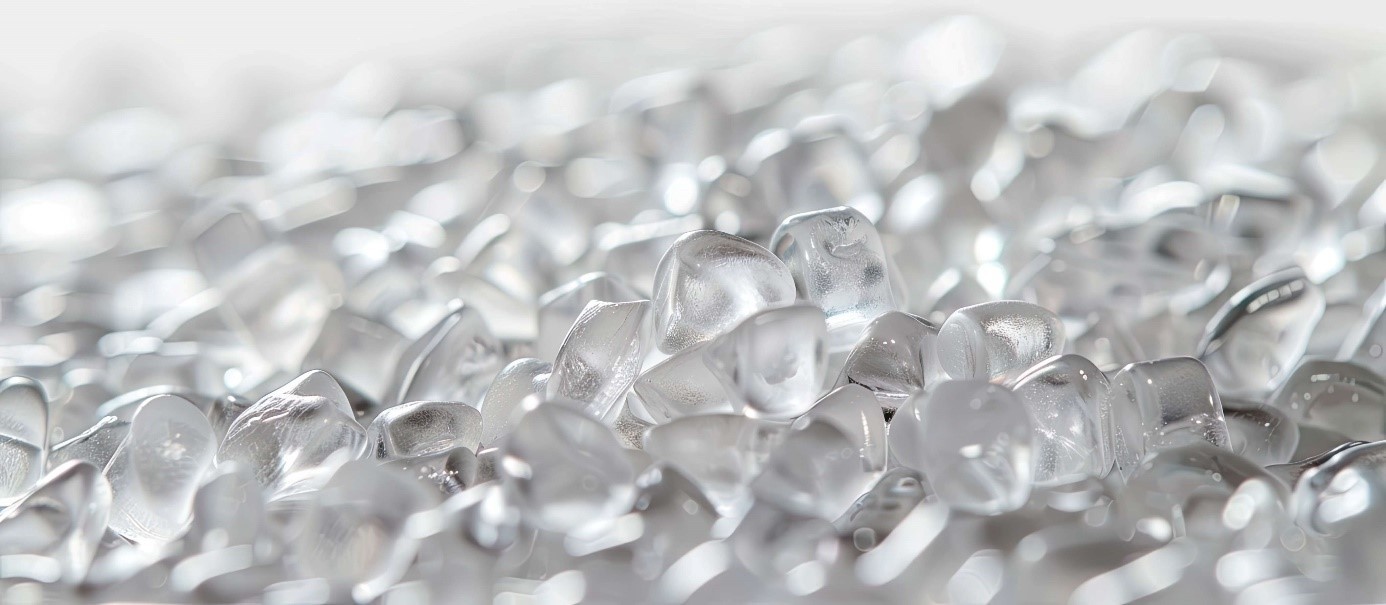
In the realm of engineering plastics, polyamide stabilization plays a critical role in ensuring the durability, performance, and lifespan of these versatile materials. Polyamides, such as PA6, PA6.6, PA11, and PA12, are known for their excellent mechanical properties and wide range of applications across multiple industries. However, without adequate stabilization, these materials are susceptible to degradation, which can compromise their structural integrity and usefulness. This degradation is often a result of thermal oxidation and hydrolysis, both of which can significantly reduce the performance of polyamides over time. In this comprehensive guide, we will delve into the mechanisms of thermal oxidation in polyamides, highlight the importance of stabilization, explore the different methods employed to extend the durability of these plastics, and examine real-world applications where stabilization has proven to be critical.
What is Polyamide Stabilization?
Polyamide stabilization refers to the various techniques and strategies used to protect polyamides from degradation caused by environmental and operational factors. These techniques ensure that the materials maintain their mechanical strength, color stability, and overall performance, even under harsh conditions. Given the importance of polyamides in industries such as automotive, electronics, and industrial manufacturing, effective stabilization methods are necessary to prevent the loss of material properties and avoid premature failure.
Importance of Polyamide Stabilization
Polyamides are widely used because of their high strength, flexibility, chemical resistance, and thermal stability. However, these materials are not invincible. Over time, exposure to high temperatures, moisture, and oxygen can trigger chemical reactions that degrade the polymer chains, leading to discoloration, embrittlement, and loss of mechanical properties. Without proper stabilization, polyamides would be rendered ineffective for long-term applications, particularly in industries where durability is paramount.
Understanding Thermal Oxidation in Polyamides
The Mechanism of Thermal Oxidation
Thermal oxidation is a chemical reaction that occurs when polyamides are exposed to oxygen at elevated temperatures. The process starts with the generation of peroxyl radicals, which then attack the polymer chains at vulnerable points, particularly at methylene groups near nitrogen atoms. This attack results in the formation of alkyl radicals, which, when combined with oxygen, produce additional peroxyl radicals. This chain reaction continues, leading to the formation of hydroperoxides that weaken the polymer structure.
The breakdown of these hydroperoxides further accelerates the degradation process, resulting in a gradual loss of mechanical properties such as tensile strength and impact resistance. Additionally, the oxidation process often causes discoloration, turning the material yellow or brown, which can be aesthetically undesirable, especially in consumer-facing applications.
Aliphatic vs. Aromatic Polyamides
There are two main categories of polyamides: aliphatic and aromatic. Both types are susceptible to thermal oxidation, but the degradation mechanisms differ slightly between the two.
- Aliphatic Polyamides: These include materials like PA6 and PA6.6, which are highly susceptible to thermal oxidation. The degradation process is initiated at lower temperatures and tends to progress more rapidly compared to aromatic polyamides. The presence of functional groups, such as carboxylic acids, can accelerate this degradation, making stabilization essential for maintaining material properties.
- Aromatic Polyamides: These materials are more resistant to thermal oxidation, requiring higher temperatures to degrade. However, once the process begins, the presence of carboxylic groups can still increase the rate of degradation. Although they offer improved thermal stability, aromatic polyamides are not immune to the long-term effects of oxidation.
The Role of Structural Irregularities
The molecular structure of polyamides plays a significant role in their susceptibility to thermal oxidation. Structural irregularities, such as uneven polymer chain lengths or the presence of impurities, can create weak points that are more vulnerable to attack by peroxyl radicals. These irregularities can amplify the effects of oxidation, leading to faster degradation.
Impact of Carboxylic Groups and Moisture Levels on Polyamide Stability
How Carboxylic Groups Accelerate Degradation ?
The presence of carboxylic groups in polyamides has been found to significantly accelerate the rate of thermal degradation. Carboxylic groups serve as reaction sites for oxidative processes, speeding up the breakdown of the polymer chains. This makes it crucial to incorporate stabilizers that can neutralize these effects, preserving the material's thermal and mechanical stability.
The Role of Moisture in Hydrolysis
Moisture also has a substantial impact on the long-term stability of polyamides. When polyamides are exposed to excess moisture, especially during processing, hydrolysis of the amide groups can occur. This process results in the breakdown of the polymer chains, reducing the material's strength and performance. For aliphatic polyamides in particular, controlling moisture levels during processing is essential for preserving their mechanical properties and preventing early degradation.
The Commercial Importance of PA6, PA6.6, PA11, and PA12
Key Properties and Applications
PA6, PA6.6, PA11, and PA12 are among the most widely used polyamides in the industry due to their mechanical strength, chemical resistance, and thermal stability. These materials are commonly used in applications such as automotive components, electrical housings, industrial machinery, and consumer electronics. However, their tendency to yellow and degrade when exposed to high temperatures requires the use of stabilizers to maintain both their appearance and performance.
Challenges in Stabilization
One of the primary challenges in stabilizing these polyamides is preventing yellowing during high-temperature processing. This is often mitigated by using secondary stabilizers, such as phosphites, which help maintain color stability while also protecting the polymer from thermal degradation.
Long-Term Heat Stabilization Methods for Polyamides
From a commercial standpoint, the most significant polyamides are PA6, PA6.6, PA11, and PA12. These materials are relatively stable during processing, with occasional yellowing issues, which can be mitigated by adding secondary stabilizers such as phosphites.
Long-term heat stabilization of polyamides is typically achieved through specific stabilization packages, which can be categorized into two main groups:
- Inorganic stabilizers: Copper(I) salts combined with iodide salts, such as copper acetate and potassium iodide, are commonly used. The optimal concentration is approximately 40 ppm of Cu+ and 1000 ppm of I-. Increasing the copper ion concentration beyond this point does not provide additional benefits, while higher iodide concentrations can lead to discoloration. A key drawback of this system, aside from discoloration, is its tendency to be extracted by water or water-glycol solutions, which are often used in cooling systems.
- Organic stabilizers: A combination of hindered phenols and phosphite avoids the discoloration issues associated with inorganic stabilizers. Phenolic antioxidants such as Euronox 10, Euronox 245, and Euronox 98, in combination with Euronox 68, are effective in preventing both yellowing and mechanical degradation. Notably, the combination of Euronox 98 and Euronox 68 in a 1:1 ratio, at concentrations between 0.3% and 0.7%, has proven to be particularly effective.
Industry Case Studies: Success in Polyamide Stabilization
Automotive Industry : In the automotive industry, polyamide stabilization has proven crucial for components that operate under high thermal stress, such as engine covers, air intake manifolds, and cooling system parts. Using advanced stabilizers, manufacturers have been able to extend the lifespan of these components, reducing the risk of failure and ensuring the long-term reliability of vehicles.
Consumer Electronics : In the consumer electronics sector, stabilized polyamides have been used to improve the durability and appearance of products such as connectors & cable, cable ties & fasteners, CEE plugs, connectors, miniature circuit breakers, switchgears, headphone components, internal phone components, and mobile protective casings. Stabilizers help maintain the material's color and strength, even after years of use, ensuring that the products remain both functional and visually appealing.
For more information, visit our product catalogue.
Conclusion
In conclusion, polyamide stabilization is a critical process for ensuring the long-term durability and performance of these versatile materials. By understanding the mechanisms of thermal oxidation, controlling moisture levels, and employing both inorganic and organic stabilizers, engineers can protect polyamides from degradation and extend their useful lifespan. With continued research and emerging technologies, the future of polyamide engineering looks bright, offering exciting possibilities for industries that rely on these essential materials.
For those looking to implement or improve polyamide stabilization in their projects, staying informed about recent advancements in stabilization technologies will be key to making informed decisions. These innovations will allow engineers to not only enhance the performance of their materials but also contribute to a more sustainable future.