Revolutionizing Rubber Compound Manufacturing with Dry Liquids
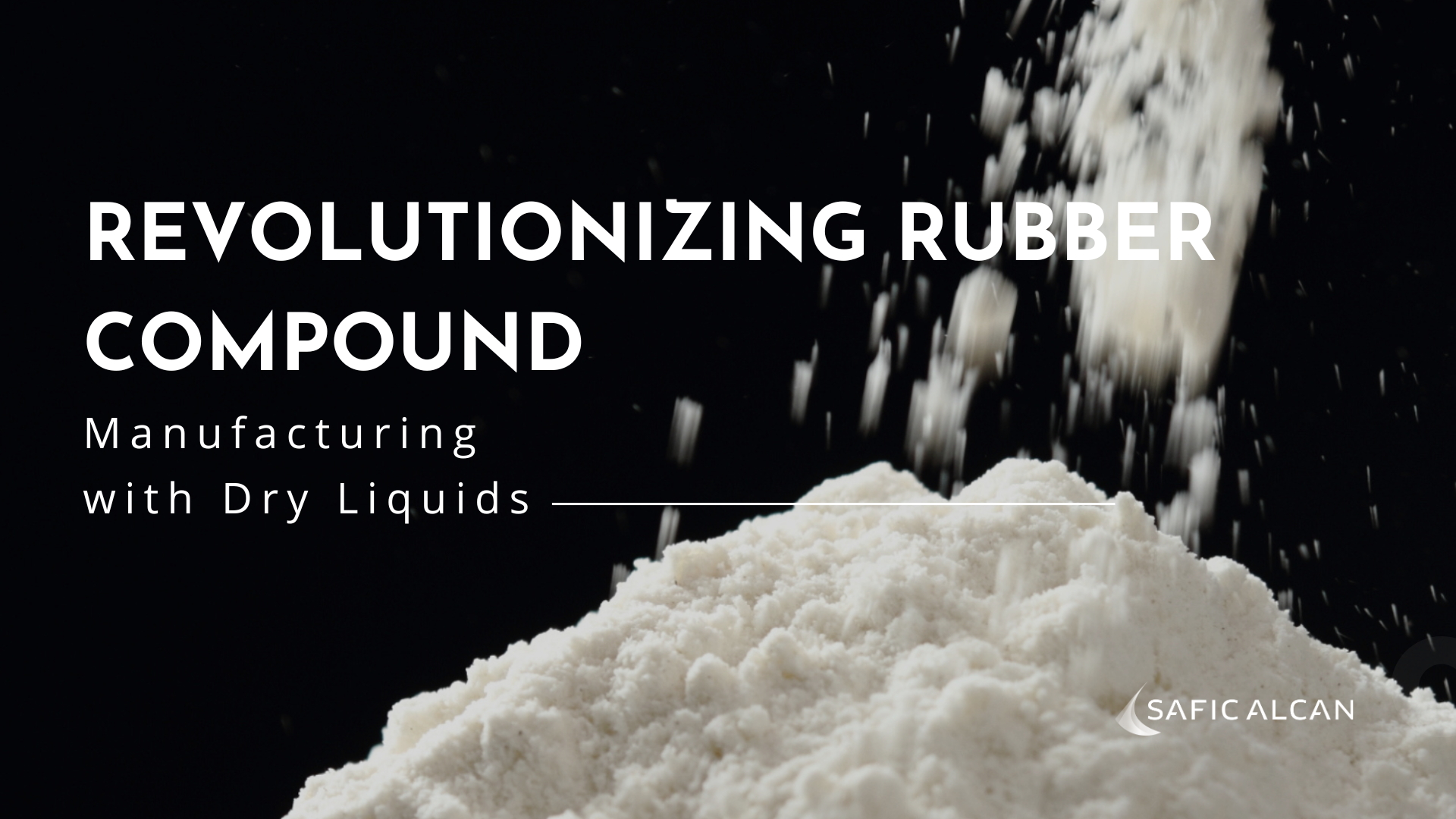
Rubber compounds play a crucial role in various industries, and they typically contain between 5 and 15 ingredients which are mixed together in an internal mixer or on a 2-roll mill in a batch process.
Typical formulations include elastomers, fillers, oils/plasticizers, process aids, anti-degradants, and curatives, with each component contributing to the desired properties of the final product. However, handling liquid ingredients in the mixing process poses significant challenges, from potential leaks and spills to difficulties in accurate weighing and disposal of containers. In this article, we explore the concept of dry liquids as a solution to these challenges.
Overcoming Challenges in Rubber Compound Manufacturing
The Complexity of Liquid Handling in Rubber Compounds
The traditional method of manufacturing rubber compounds involves the use of liquids. High-volume liquids are usually handled by automatic weighing and injection systems, but small to medium volume liquids are usually delivered in heavy drums or Intermediate Bulk Containers (IBLCs).
These containers often present difficulties in transportation to the weigh station, and the taps on drums and IBLCs can lead to leaks and drips that are hard to clean up. Additionally, the residue left on jugs and scoops poses a risk of cross-contamination. Liquids with varying viscosities, melting points close to ambient temperatures, or high volatility add further complexity to the weighing process.
Introducing Dry Liquids: A Game-Changing Solution
What Are Dry Liquids?
Dry liquids offer an innovative solution to the challenges associated with handling liquid ingredients. A dry liquid is essentially a blend of powder and liquid, presented in a solid, powder form. Precipitated silica is a commonly used powder carrier due to its high absorbency, compatibility with rubber compounds, and cost-effectiveness. A silica/liquid blend can result in a free-flowing powder containing up to 75% liquid content. Other carriers such as calcium silicate or carbon black can also be employed.
Key Benefits of Using Dry Liquids in Manufacturing
The use of dry liquids in rubber compound manufacturing offers a transformative solution to liquid handling challenges. By enhancing accuracy in weighing, reducing the risk of contamination, improving housekeeping, and eliminating the issues associated with drum disposal, dry liquids contribute to a more efficient and streamlined manufacturing process.
Materials Best Suited for Dry Liquids
Cyanurates Coagents (TAC/TAIC)
These materials, with melting points at or close to room temperature, are challenging to handle in liquid form. Converting them into dry liquids simplifies the weighing process.
Liquid Polymers
Typically, high viscosity, these materials often require heating to become mobile enough for weighing. Dry liquid versions facilitate easier handling. Examples include Liquid NBR, Polysulphide and Butadiene.
Plasticizers
When not included in an automatic weighing and dosing system, dry liquid versions of plasticizers, such as VULCOFAC DOS DL70, improve manual weighing processes. Factice can be used as a carrier in soft compounds where silica addition is not desirable. Dry liquid versions of plasticizers are particularly useful when open mill mixing as they are much easier to incorporate into the mix.
Methacrylate Co-agents
Viscous liquids used in small quantities per batch, these materials benefit from the conversion to dry liquids, eliminating handling issues. For example, VULCOFAC TMPTMA DL50, VULCOFAC TMPTMA DL70 and VULCOFAC TMPTMA R DL75.
Liquid Anti-degradants and Curatives
These can be easily converted into dry liquids, simplifying handling and weighing processes. These include VULCOFAC ACT55 which was specifically developed to replace more hazardous accelerators used in speciality elastomers.
SAFIC-ALCAN’s Expertise in Dry Liquid Production
The History of Dry Liquid Manufacturing at SAFIC-ALCAN
SAFIC-ALCAN started producing dry liquids in 1992 at its factory in Warrington, a town located between Manchester and Liverpool in England. Since then, SAFIC-ALCAN has developed strong expertise in the conversion of liquid to powder and can transform more or less any type of liquid to powder.
Overview of Available Dry Liquid Grades
Today, more than 100 different grades of dry liquids are available in our portfolio, for example:
- VULCOFAC EGDMA DL70, VULCOFAC TMPTMA DL70, VULCOFAC TAIC DL70, VULCOFAC TAC DL70 - coagents for peroxide cure
- VULCOFAC 69 DL70, VULCOFAC 172 DL50, VULCOFAC 6498 DL70 - silane coupling agents
- VULCOFAC BLW DL70, VULCOFAC 705 DL70 - antioxidants
- VULCOFAC ACT55, which is is recommended for the replacement of guanidine accelerators (especially DOTG) as safer alternative and it is used mainly for AEM and ACM compounds. VULCOFAC CP3441, VULCOFAC ZAP - special accelerator preparations (offering safety solutions for customers)
- VULCOFAC RRP DL - used as a bonding agent
- VULCOFAC PLCT DL70 - coumarone resin used as a tackifier
This is a small snapshot of the grades available. Based on constant demands from customers, new dry liquids are developed every year by our team in the UK.
Commitment to Innovation and Sustainability
Developing Eco-Friendly Alternatives
Our commitment to innovation ensures that we stay ahead of industry trends and meet the evolving needs of our clients. Each year, our dedicated technical teams work to create new formulations that enhance performance and efficiency as well as sustainable advantage.
For instance, we are currently exploring eco-friendly alternatives that not only meet regulatory standards but also reduce environmental impact. This initiative reflects our dedication to sustainability and our responsibility towards the planet.
Customer Support and Technical Assistance
In addition to expanding our product range, we also prioritize customer support. Our technical experts are always available to assist clients in selecting the right products for their specific applications. Whether it's for automotive, construction, or industrial uses, we aim to provide tailored solutions that drive success.
Furthermore, we regularly conduct training sessions and workshops to keep our customers informed about the latest advancements in our product offerings. This ensures that they can make the most of our dry liquids and apply them effectively in their processes.
The Future of Rubber Compound Manufacturing with Dry Liquids
Continuing Innovation and Product Development
As we look to the future, we remain committed to quality, innovation, and customer satisfaction. We believe that by working closely with our clients and understanding their challenges, we can continue to develop products that not only meet but exceed their expectations.
Meeting Customer Needs in a Dynamic Industry
To learn more about how our dry liquid solutions can revolutionize your rubber compound manufacturing process, get in touch with our team today.
Download the technical data sheet (TDS) and request a sample directly from our online catalog.